Case Study
Custom-Engineered Bearing Isolator and Commitment to Customer Seal the Deal at Arizona Copper Mill
Application: Gearbox
When Bill Kuczynski from Casey Industrial noticed a large amount of oil leaking from a gearbox on a sag mill at a client’s copper milling facility, he knew it was time to recommend a permanent sealing solution. Kuczynski, an Outside Services Manager for Casey Industrial, regularly visits the mill to monitor equipment and advise the client on when to perform maintenance. He recalled ongoing leaks and related maintenance issues with this gearbox during the 10 years he has visited the mill. The gearbox used lip seals which tend to have a short and unreliable service life due to using contact with the shaft to retain lubrication. Lip seals wear at the point of contact or groove the shaft causing lubrication loss and contamination ingress.
The rising costs associated with using low-cost lip seals were becoming apparent at the mill. The lip seals needed to be replaced every three to six weeks. This repair became very time-consuming and expensive because it could only take place during scheduled downtime, it required three maintenance personnel to repair, and it took 3-4 hours to complete.
Furthermore, the gearbox was in a confined location that limited access to the shaft, complicating the already high-cost repair. Between scheduled maintenance, the leaking gearbox caused a costly, messy and hazardous problem that was also an environmental concern. Large amounts of oil were being wasted as it leaked directly to the deck below the gearbox, causing a slip hazard. In addition, workers had to add oil each shift to replace what was being lost because of the leak.
Solving the Challenge
High oil levels and oil splash make gearboxes notoriously difficult to seal, especially in industrial rotating applications. Inpro/Seal’s sealing solution for the gearbox is based on the patented VBXX-D Bearing Isolator. This is a non-contacting, compound labyrinth seal that consists of a stator and a rotor. The stator has a large D Groove that captures oil attempting to flow down the shaft out of the housing. Through a drain port, the captured oil is channeled back to the gearbox oil sump. The rotor prevents outside contaminants from entering the gearbox by collecting them in the labyrinth design. Centrifugal force then expels the captured contaminants to the outside environment. The result is a permanent, non-contacting seal that efficiently keeps the lubricant in the gearbox. It also prevents outside contaminants, such as water and dirt, out of the gearbox bearing housing.

Eliminate Leakage with an Air Seal
An operational flood in the bearing housing compounded the sealing challenge for the SAG mill gearbox. Unlike most gearboxes that splash oil into the bearings, the gearbox on the SAG mill pumped oil into the center of the double-row spherical roller bearings. This ensured continuous lubrication to the bearings and also tended to throw the oil toward the lip seal. The oil that was attempting to flow back through the bearings to return to the sump was impeded, creating an operational flood. This placed additional pressure on the lip seal and increased their failure rate. A permanent solution needed to perform in an operational flood and be installed on-site without decoupling equipment.
Inpro/Seal modified a standard VBXX-D Bearing Isolator to fit the gearbox's unique challenges. This custom-engineered design included:
- A split to allow seal installation without decoupling equipment.
- A larger D Groove to capture the volume of oil flowing through the system.
- An external drain and revamped system to return oil to the sump.
Inpro/Seal’s custom-engineering expertise was the key to designing the permanent sealing solution. The Inpro/Seal team had experience with all of the factors, including size restrictions, lubrication type, bearing type, and flooded applications.
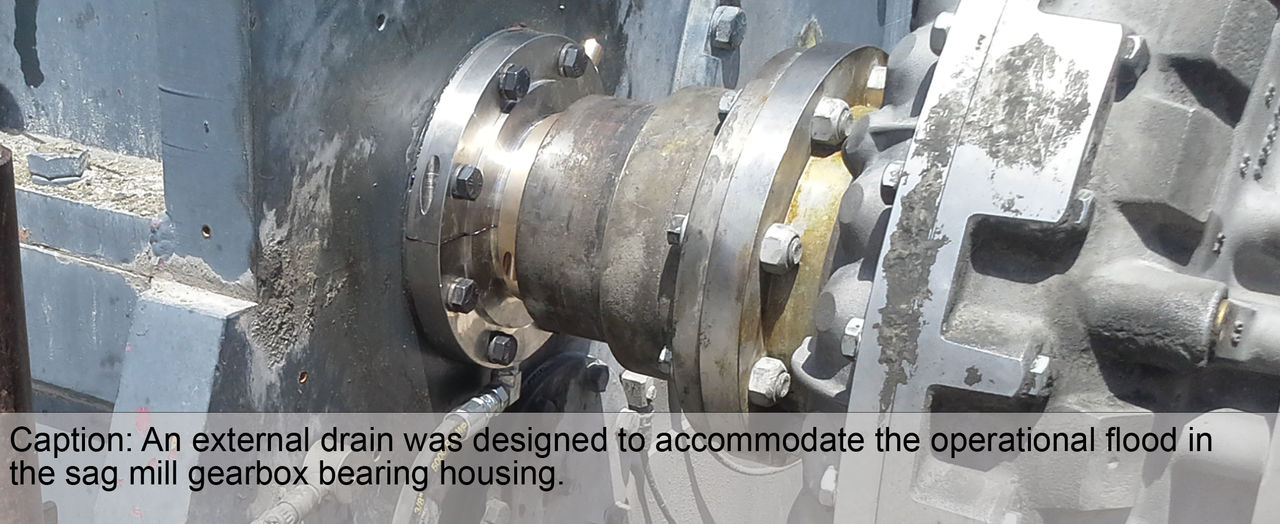
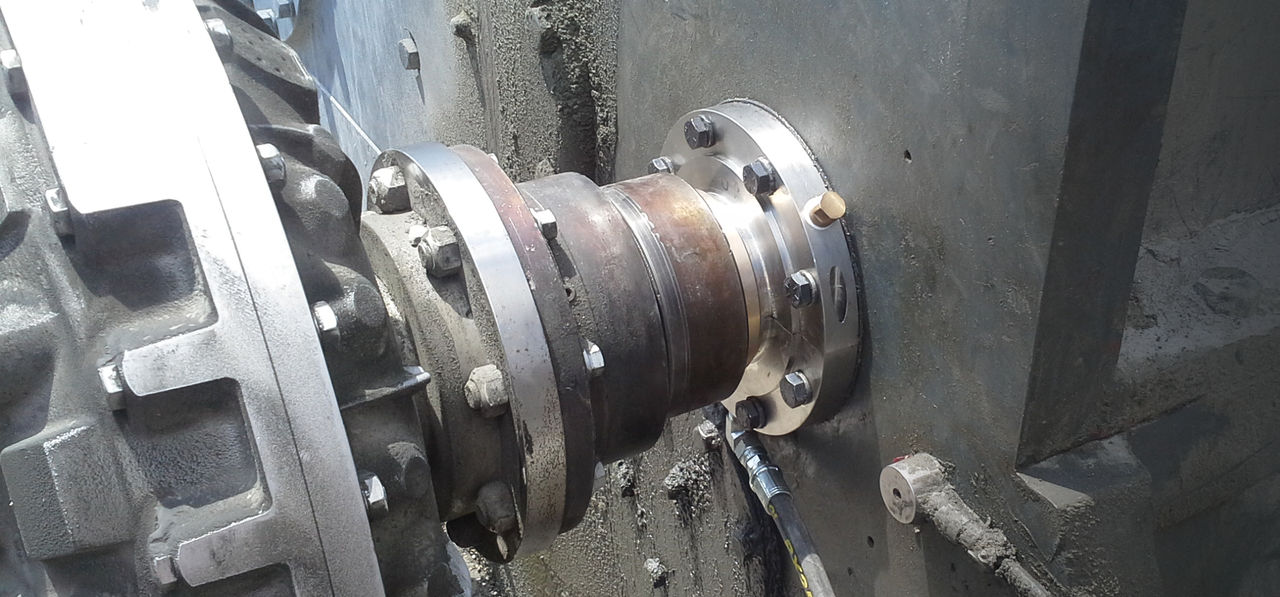
Success Summary
The time and costs associated with maintaining this gearbox were greatly reduced because the customized seal and drain back system provided a permanent sealing solution. Less maintenance results in more production time and lower costs for the SAG Mill – along with a safer working environment.
The two Inpro/Seal Bearing Isolators installed on this gearbox have been in operation for over two years. According to Kuczynski, “Everything continues to perform as expected, without any signs of a leak.” He added that Inpro/Seal continues to check in to monitor the performance of the bearing isolator. “That’s the thing about Inpro/Seal – they don’t walk away after the install.”
Advantages of Bearing Isolator Installed on a Sag Mill Gearbox
- Custom engineered to provide permanent bearing protection.
- Uses a split design for installation without decoupling the equipment.
- Utilizes an external drain and revamped oil return system to accommodate an operational flood in the bearing housing.
- Increases production, decreases maintenance costs, and provides a safer working environment.
Ready to Get Started?
Count on us to improve equipment reliability through permanent bearing protection. No matter the size or complexity of the application, Inpro/Seal’s technical experts can design a custom solution for your equipment. With over 40 years of experience, we are the trusted source of Bearing Isolator technology.